Por ahora se trata solo de un proyecto piloto, pero el aumento de la productividad en un 20%. Esto permite augurar futuro a la fabricación modular flexible, que podría suponer el fin de la cadena de montaje tradicional y sus cintas transportadoras
Durante más de un siglo, desde que Henry Ford adaptase en 1913 a la fábrica del Model T en Detroit una imaginativa solución que había visto poco antes en su ciudad, la cinta transportadora ha marcado el ritmo de la producción de automóviles. De la noche a la mañana, la planta de Ford pasó de 100 a 1.000 coches diarios, y si antes se necesitaban 12 horas para completar un vehículo, la primera cadena de montaje moderna permitió reducir ese tiempo a 93 minutos.
Pero actualmente se están alcanzando los límites de este sistema… Pues la cantidad de versiones y las posibilidades de personalización han hecho crecer mucho las configuraciones potenciales. Un sistema de ensamblaje basado en una cadena de montaje o cinta transportadora convencional se adapta cada vez peor a las nuevas necesidades… Ya que ese trabajo está basado en un principio de tiempo uniforme para cada producto en cada puesto de trabajo y en una secuencia fija.
Caracteristicas de “Audi”
Por ello la automotríz Audi está trabajando en un sistema de ensamblaje modular, el primero de este tipo en la industria del automovil y revolucionaría todo. Porque con el nuevo método modular y flexible los trabajadores ensamblan los componentes en las llamadas ‘islas de producción’, con independencia del ciclo productivo general. Además, los vehículos de guiado automático (AGV por sus siglas en ingles) y robots moviles autonomos (AMR, de nuevo, por sus siglas en ingles) se encargan de suministrar a las estaciones de trabajo los materiales necesarios, de acuerdo con la estrategia ‘good-to-person’, en el que cada pieza o módulo llega directamente al operario a través de sistemas automatizados.
Por ello Audi lleva tiempo trabajando en un sistema de ensamblaje modular que, de convertirse finalmente en realidad, sería el primero de este tipo en la industria del automóvil y revolucionaría la organización de las factorías. Porque con el nuevo método modular y flexible los trabajadores ensamblan los componentes en las llamadas ‘islas de producción’, con independencia del ciclo productivo general. Además, los AMR y AGV se ocupan de suministrar a las estaciones de trabajo los materiales necesarios, de acuerdo con la estrategia ‘good-to-person’, en el que cada pieza o módulo llega directamente al operario a través de sistemas automatizados.
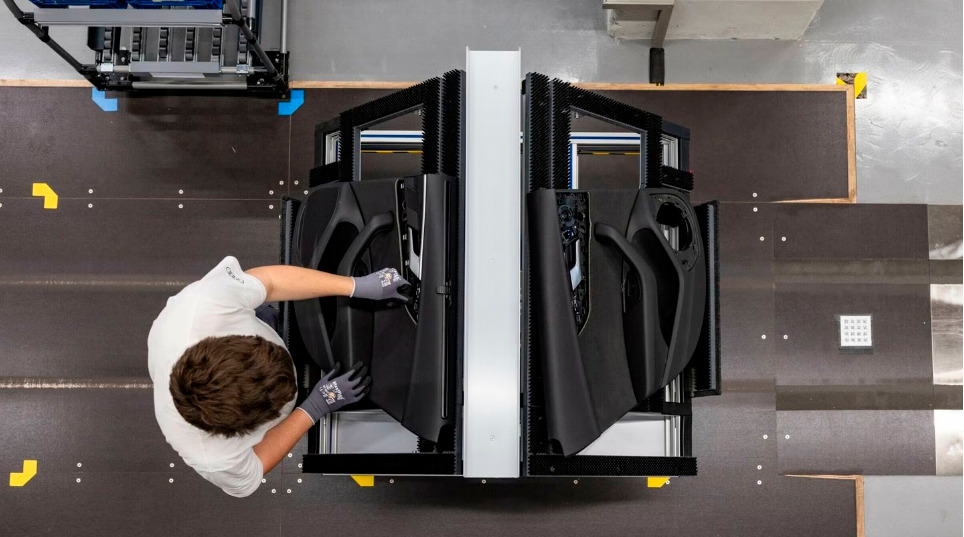
Ventajas de “Audi”
Los procedimientos dinámicos se desplazan a una secuencia variable de estaciones y tiempos de procesamiento, lo que podríamos definir como cinta transportadora virtual. Como preparación para su posterior aplicación a la fabricación en serie, el equipo de Wolfgang Kern, director de Proyectos en el Laboratorio de Producción de Audi (P-Lab), está aplicando este concepto en el premontaje de paneles interiores para las puertas en la planta de Ingolstadt. Se explica que utilizan “la tecnología digital para simplificar el trabajo a los empleados y mejorar la flexibilidad y la eficiencia en la producción”.
Otra ventaja fundamental del sistema flexible es que Audi puede emplear a personas que ya no pueden trabajar en la línea debido a limitaciones físicas. “Podemos adaptar el entorno de trabajo a sus condiciones, lo que actualmente sólo es posible de forma muy limitada en la cinta transportadora. Recurrimos a una automatización más flexible en el proceso de producción para aliviar la carga de las personas”, explica Kern. Todos los empleados se benefician de una carga de trabajo más ligera gracias a esto, lo que permite una adaptación ergonómica a las necesidades individuales.
Josef Weinzierl añade: “El montaje modular no es un fin en sí mismo, y no es el único sistema de calidad. Pero sí amplía nuestro abanico de herramientas para responder a los futuros retos de la fabricación de vehículos. La cadena de montaje seguirá existiendo en el futuro… pero se está acercando cada vez más a sus límites. Sobre todo en la fase de premontaje, y por eso necesitamos nuevas soluciones que aporten mayor flexibilidad”.
Los AGV deciden sobre la marcha
En la fase de pruebas, las tareas ya no siguen una secuencia uniforme, pues se estructuran para satisfacer necesidades concretas. Los vehículos de guiado automático (AGV) trasladan los paneles de las puertas directamente a la estación en la que hay que montar los componentes. Por ejemplo, los conjuntos de iluminación se instalan con el cableado y otros elementos en una estación… Los trabajos que no necesitan estos conjuntos se saltan esa estación.
En otra estación, un trabajador instala las cortinillas que la marca ofrece para las puertas traseras como opción. Debido a su ritmo predefinido, en la cinta transportadora esta tarea tendría que repartirse entre dos o tres trabajadores… Lo que resulta ineficiente y puede poner en peligro la calidad del producto. Si los trabajos se acumulan, los AGV conducen el producto a la siguiente estación necesaria con el menor tiempo de espera posible. Además, la configuración de los espacios de trabajo se comprueba y ajusta regularmente.
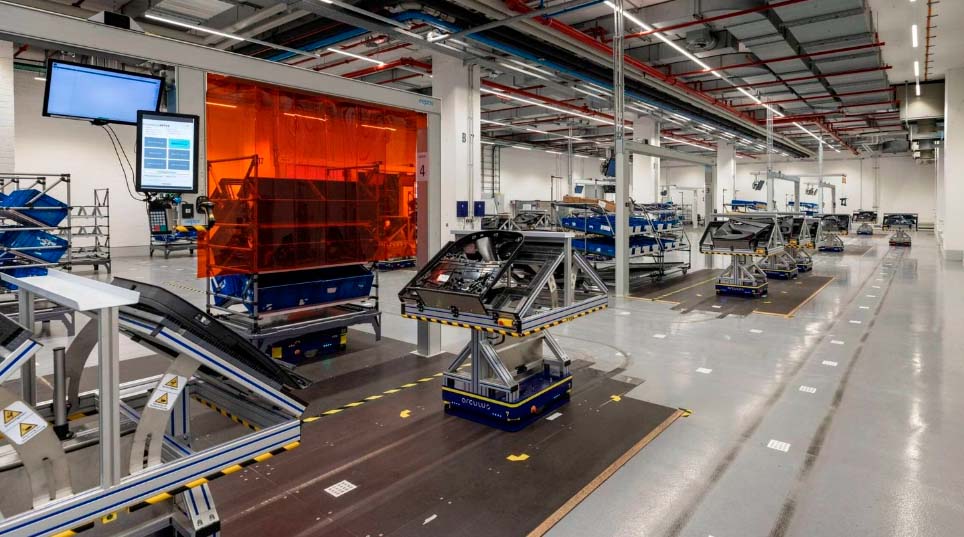
“En comparación con la organización actual, la flexibilidad que se logra con el nuevo sistema de guiado supone un avance esencial”, defiende Kern. A diferencia de una cinta transportadora, las estaciones individuales y el sistema de producción modular no están diseñados para satisfacer una demanda estable, sino que pueden funcionar de forma eficaz con una gama de alternativas determinada. Kern afirma que “gracias a las estaciones independientes, la producción puede adaptarse con más facilidad a cada trabajador. Esto se aplica a la fase de formación, a las operaciones en curso y a la adaptación de los empleados con necesidades específicas. En general, estamos mejorando el trabajo de producción convencional y haciéndolo más flexible. Podemos realizar todo un paso de producción en una estación o adaptar individualmente tanto el espacio de trabajo como los tiempos previstos; y los vehículos de guiado automático también nos aportan ventajas ergonómicas”.
El principio ‘good-to-person’
Cuando la variabilidad de los componentes es alta, el principio ‘good-to-person’ es la solución idónea. Por ejemplo, cuando los AGV transportan los arneses de cables que los trabajadores necesitan para los paneles de las puertas, los operarios cogen solo las piezas que necesitan, y el resto de componentes idénticos vuelve a la posición de espera, puesto que normalmente se necesitará una variante distinta para el siguiente panel de puerta.
El suministro de piezas clasificadas a través de los AGV permite que no tenga que hacerse una separación previa, y los vehículos están geolocalizados al milímetro mediante una red de radio, controlando su guiado en todo momento un ordenador central. Además, la inspección por cámara también puede integrarse en el proceso de calidad, y las posibles irregularidades en la fabricación se pueden gestionar de forma más rápida y sencilla que en una cinta transportadora, lo que ayuda a evitar trabajos adicionales imprevistos.

Siempre que tengamos un alto grado de variación en los componentes, los métodos convencionales de suministro de materiales ya no son suficientes. En el concepto de montaje flexible la selección exacta de los productos necesita una gran antelación, lo que requiere automatizar aún más el proceso logístico, que también ofrece mucho potencial de ahorro”, explica Kern.
La productividad aumenta un 20%
El proyecto piloto de Audi está aportando conocimientos valiosos y permite a los ingenieros ensayar algunas aplicaciones en la fabricación en serie. “Al reducir el tiempo de producción mediante una orientación hacia la creación de valor y la autodirección, somos capaces de aumentar la productividad en aproximadamente un 20%”, afirma Kern. El siguiente paso será integrar un sistema de ensamblaje modular a mayor escala en la fase de premontaje. Debido a que es en ese proceso donde se da una mayor variabilidad y un dinamismo que se puede gestionar con más eficacia. “La desvinculación de las estaciones permite reprogramar los procesos sin mucho esfuerzo”, explica Kern, ya que gracias al hardware flexible y a los robots, a menudo sólo hay que ajustar el software, y las estaciones pueden adaptarse a los productos y a la demanda con más facilidad que con una cinta transportadora clásica.
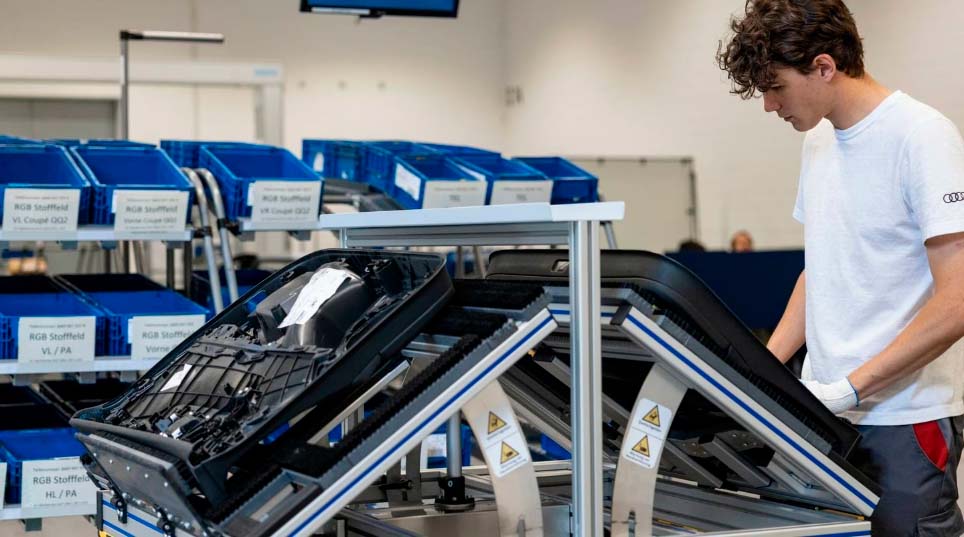
En cuanto a los siguientes pasos y la potencial aplicación futura del nuevo sistema productivo, Josef Weinzierl se muestra prudente: “Nuestro proyecto piloto está demostrando que el montaje modular cumple los requisitos de estabilidad, idoneidad para nuestros trabajadores y disponibilidad para la producción en serie; y estamos estudiando las áreas de aplicación en las que podamos implantar nuestro sistema de forma viable en el futuro. Pero tenemos que pensar detenidamente en ese paso, porque no hay vuelta atrás. En cualquier caso, podríamos estar utilizando el ensamblaje modular en la fase de premontaje de un vehículo nuevo a partir de 2025″.
Fuente: https://www-elconfidencial-com.cdn.ampproject.org/c/s/www.elconfidencial.com/amp/motor/tecnologia-y-motor/2022-08-29/audi-modular-flexible-factoria-cadena-industria-fabricacion_3481810/